Precise, informative and reliable testing of aeronautical components for industry and academia.
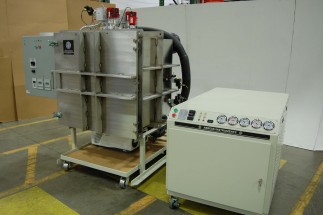
Our aeronautic component testing systems provide a platform for component testing which enables the user to precisely and easily control the test conditions of the system as well as log-data concerning the article under test.
Using thermal vacuum cycle controllers (VCC) and a Snow River ® Cascade Heat Exchange, this system is capable of consistently achieving and maintain temperatures in the range of +200C to -96C.
To get an accurate quote for the system you need fill out our RFQ or call today!
Major components of this Aeronautic Component Test System are the following:
- Vacuum Chamber – A Front Loading 36″ x 36″ x 36″ Stainless Steel Chamber. The interior of the chamber is Electropolished to facilitate cleaning and attaining HV High Vacuum.
- Vacuum Pumping System
- Thermal Platen and Shroud System— Nickel Plated Copper Thermal Plate and Aluminum Shroud with resistance cartridge heating elements and Thermal transfer fluid piping engaged in the under surface of the thermal test platen and outer surfaces of the shroud, with thermocouple monitoring and temperature control via PID and limit Controllers.
- Pressure Gauge- Pressure transducer and controller provide pressure feedback to inform the operation of the pumps. Gauge is capable of reading pressure ranging from 3.75 x10-9 to 750 torr.
- Control Valves- Electromechanical Foreline Valves, Electromechanical Chamber Vent Valve, and Electromechanical Chamber Purge Gas Vent Valve
- Abbess Snow River ® Cascade Heat Exchange – The Ultra-Low Temp Cascade System is designed to achieve and sustain set point temperatures between 200 and -90oC within the bath reservoir. Plate temperatures are controlled by circulation of thermal transfer fluid flowing through the piping on the Thermal Platen and Shroud. Fluid flow controlled by a valve within the Snow River ® Chiller.