Systems designed and engineered to simulate space environments.
Abbess Space Simulation Chambers and Systems provide an integrated solution for recreating space conditions. During Prototyping, Flight Qualification, and Flight Verification phases, Space Simulation Systems are vital, and Abbess Instruments has an extensive portfolio of Space Simulation Test systems capable of simulating a variety of deep space vacuums with or without thermal control for use during these phases.
Before launch, instrumentation and systems must be exposed to space-like temperatures and vacuum levels, and be shown not only to survive the extreme ranges but also to operate within parameters. To prove reliable in these multivariable environments, it is required that the article under test are exposed to conditions ranging from launch through altitude increase, then into deep space followed by re-entry into a specified atmosphere. Space simulation chambers are critical to these tests, and Abbess Instruments is one of the few companies in the world with the capability and experience to manufacture these fully functional and integrated systems.
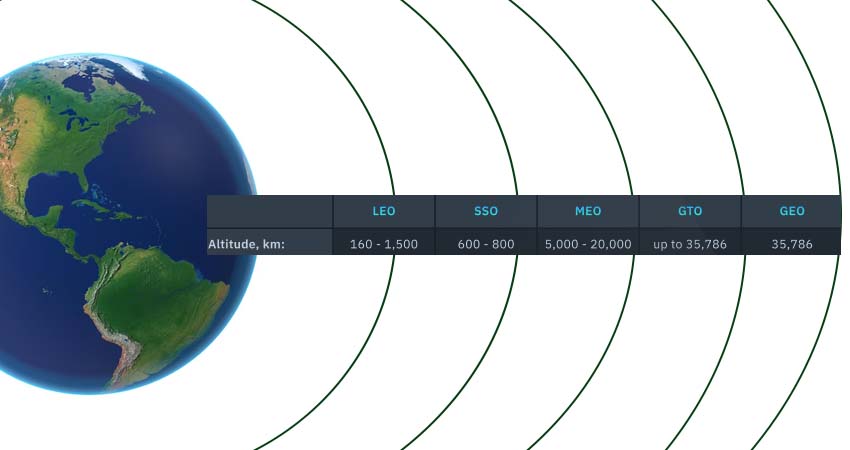
- low Earth orbit (LEO)
- Sun-synchronous orbit (SSO)
- medium Earth orbit (MEO)
- geostationary transfer orbit (GTO)
- geostationary orbit (GEO)
Please refer to our Altitude & Atmosphere Test Systems page for required testing pressures from 760 torr to 0.1 Torr (altitudes of up to 200,000 ft)!
If there is a thermal component in your test visit out Thermal vacuum System page!
To get an accurate quote for the system you need fill out our RFQ or call today!
Basic System | Complex System | Upgrade Options
View our Space Simulation Products
Basic System
A basic Space Simulation Test System consists of the following:
- Vacuum Chamber
- A front or top-loading Aluminum or SS cube with metal door
- Digital pressure gauge
- Roughing Pump w/ accompanying deep vacuum pump
- Thermal Plate to simulate temperatures often experienced in space environments
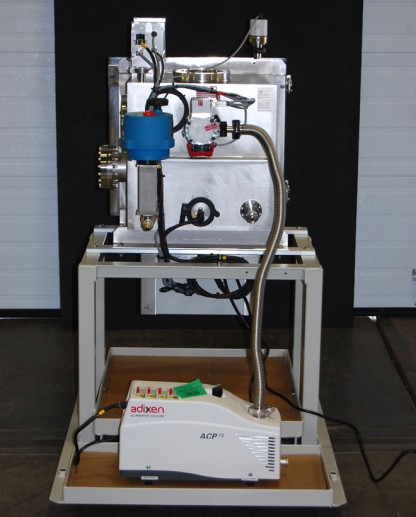
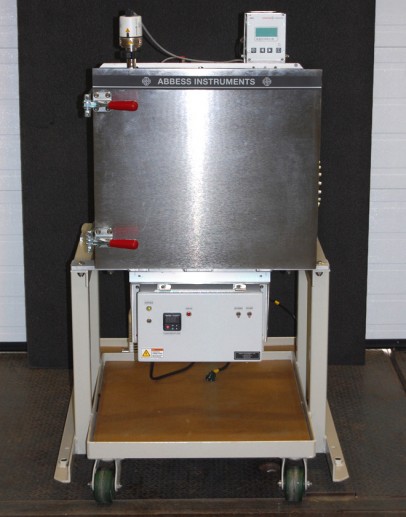

Actual chamber material choices are dependent on the desired operational vacuum, as outlined in the table below. Do you require manual or automatic operation? Abbess will work with you to customize automation to your process, just as we will work with you to ensure the system configuration meets your operational needs: While the most basic system can be controlled manually (by starting/stopping the pump(s) and opening/closing valves), a Vacuum Cycle Controller (VCC) can be added to automate the process.
There are many Upgrade Options available that will add complexity and functionality. These options, can be found in the upgradable options section down below.
Material* | Useful Pressure Range (Torr) | Use | Comments |
Untreated Al with Al or Acrylic door | 760 to 10-4 inc. | altitude testing | More powerful pumps will be needed with an Acrylic door than if a metal door was used. Acrylic door must be kept below 135C. |
Acid-etched Al chamber & door | 760 to 10-5 inc. | space simulation | |
Untreated SS chamber & door | 760 to 10-6 inc. | ||
Electropolished SS chamber & door | 10-6 and better | ||
Bakeout & Electropolished SS chamber & door | 10-7 and better | Bakeout required to outgas chamber |
To get an accurate quote for the system you need fill out our RFQ or call today!
Complex System
With precise thermal and vacuum control, the Abbess Satellite Testing Vacuum (TVAC) System is ideal for ensuring the compliance of your product or satellite to sustain ultra-high and low atmospheric conditions. Abbess designs rugged equipment and practical systems for continuous and demanding analytical, manufacturing, and production use, with safety and long life in mind. Additionally, we offer various coating for solar simulation and other orbital variables.
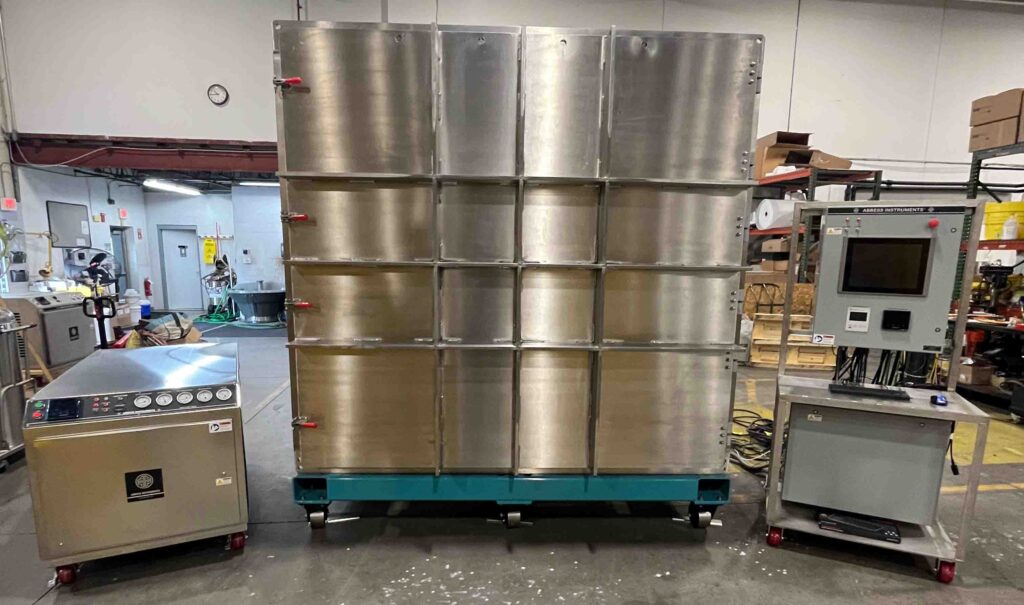
The chamber is fitted with an internal shroud which can be cooled down to LN2 temperatures or
heated up to 150degreeC with a minimum internal volume of 77in (H) x 72in (D) x 82in (W). The
chamber features three large DN500 ports, one located on top and one on each side. The TVAC system will sit on vibration isolators which will then be mounted to a optical table test setup.
Satellite Testing Vacuum System Features(TVAC):
- Vacuum Chamber (as shown above) – A Front Loading Stainless Steel Chamber with a right hinged Stainless Steel door. The interior of the chamber is Electropolished to attain high vacuum.
- Vacuum Pumping System – Through the use of any desired vacuum compatible pumping package. The package that was used on this device was three Leybold Turbo pumps and three Leybold dry roughing pumps to achieve a vacuum pressure of 10-7 Torr.
- Thermal Platen System – AeroGlaze® Coated Aluminum Thermal Plate with resistance cartridge heating elements and refrigeration media piping engaged in the under the surface of the thermal test platen.
- Thermal Shroud System – 5 sided AeroGlaze® coated Aluminum thermal plate with resistance cartridge heating elements and refrigeration media piping embeded in the back of each shroud. Thermocouple monitoring and temperature control via PID controller.
- Pressure Gauges/Pressure Transducers
- Control Valves
- Electromechanical Foreline Valve – Seperates the chamber and Turbo from the Roughing pump when venting the Chamber.
- Electromechanical Chamber Vent Valve – Gross venting valve.
- Electromechanical Chamber Purge Gas Vent Valve – Connected to the gas purge kit to allow dry nitrogen purge into the chamber.
- Gas Purge Kit – A set of preconfigured regulators, pressure relief valve, and gauges provide a controlled release of gas into the chamber.
Perform your test in-house for decades to come with this modifiable and upgradeable Satellite Testing Vacuum System(TVAC):
Benefits:
- Highly developed simulation and data collection touch screen system
- Custom user interface that is configured to custom specified equipment on your system including thermal controls
- Plot and save data, settings, and profiles
- Editable PID configuration with auto-tuning capabilities
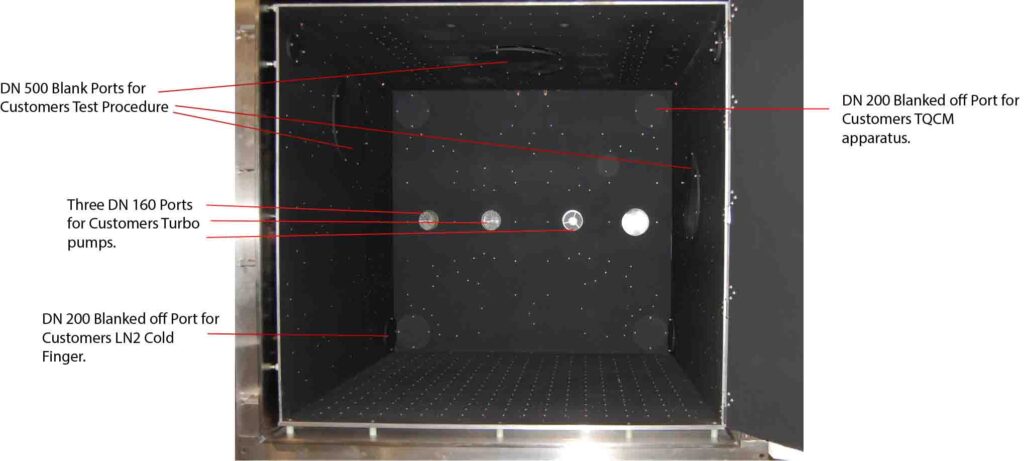
CUSTOM TOUCH SCREEN/PC VACUUM CYCLE CONTROLLER
Customized PC and Touch Screen User interface.
Allows controlled Start/Stop control of vacuum system, process, sequence, position, pressure and/or temperature monitoring and setpoint control.
Includes:
- Custom User Interface design, requires custom sequence
programing option - Custom NEMA/Work station
- Serial/USB PC interface
- Data Acquisition Interface
- Data Logging and batch records
- Many data output options
- Integration with pumps, valves, and other controllers
- With Vacuum pump relay options
PANEL PC,
- 15″ CAPACITIVE TOUCHSCREEN,
- WINDOWS 10
- Provides I/O for RS485, USB, and rs232 devices
- DUAL LAN
- MINIMUM 32GB 2.5″ SSD
- MINIMUM 4GB SO-DIMM DDR4 2666
A PC Touch Screen Vacuum Cycle Controller is a custom built system. Each Touch Screen Controller is programmed for the customer’s specific procedure.
Below is an example of what the GUI will look like:


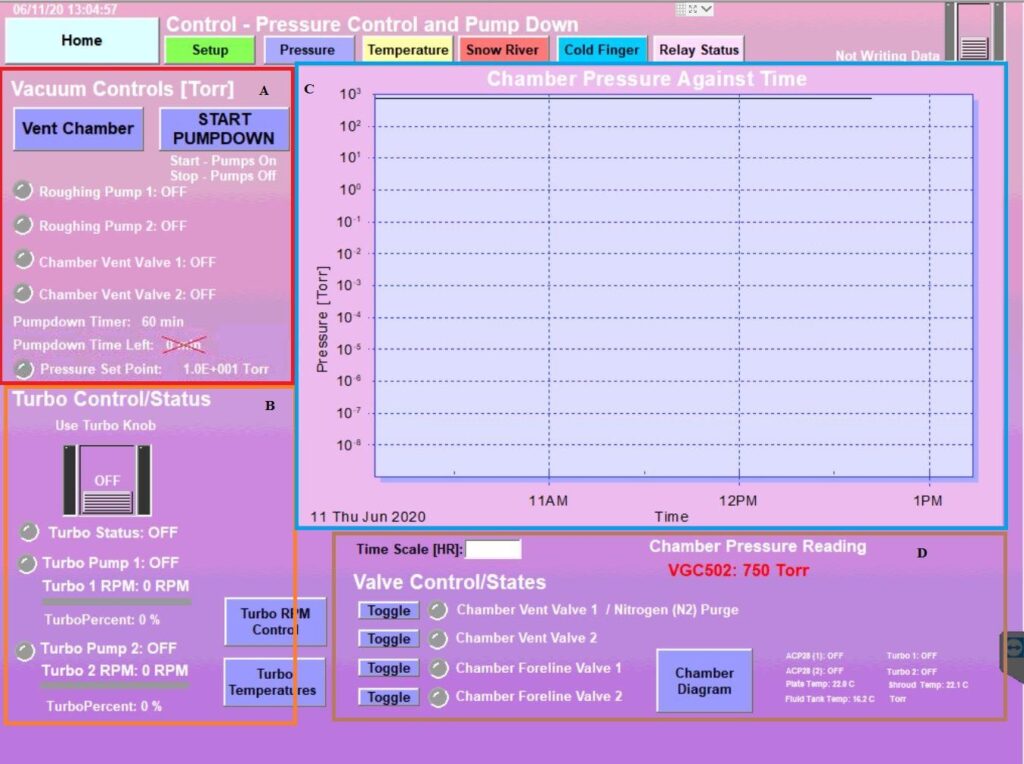


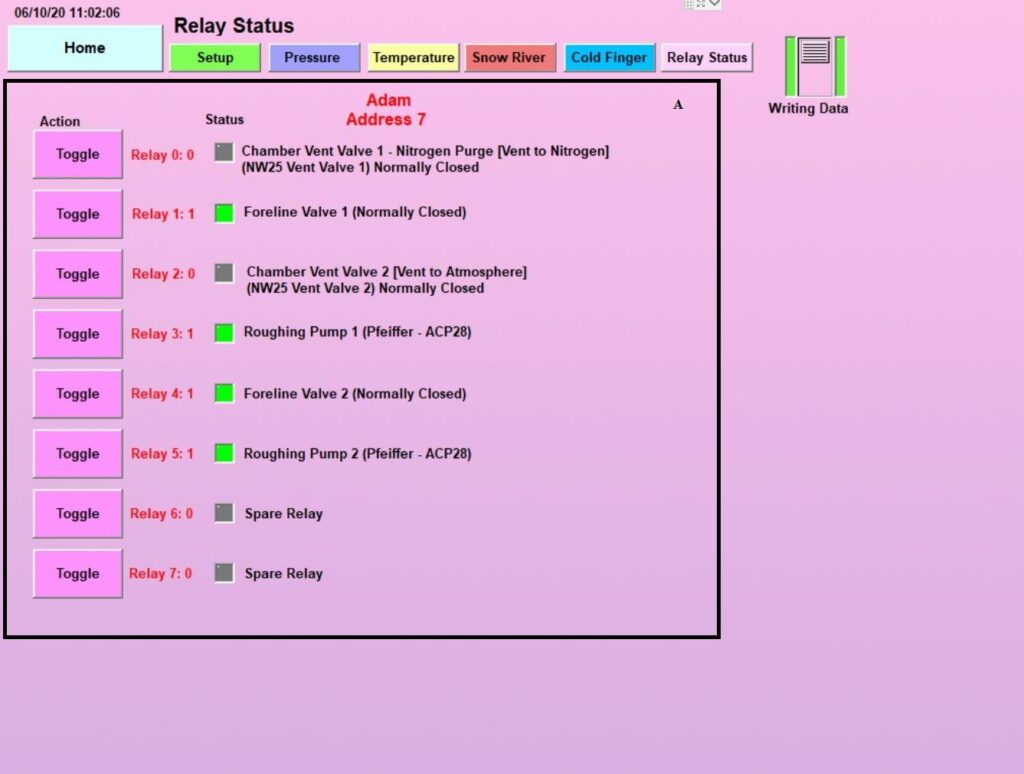
Upgrade Options
Upgrade options include:
- Vacuum Pump with Inlet and Exhaust Filters- Optional power and automatic control can be integrated into a Vacuum Cycle Controller (VCC).
- A Vacuum Cycle Controller (VCC) that can be used to automate some or all of the control functions via panel-mounted buttons and indicators (Fig 2). It will permit a single ‘automatic’ altitude/vacuum set point.
- A VCC controlled by a PC with a user-specified Graphical User Interface (GUI) operated through a touch-screen (as illustrated in Figs 3 & 4 and in Data-Logged High Vacuum Storage System). This permits: automatic monitoring, data-logging, and vacuum environment display; remote access; and optionally message-sending to operator’s mobile device.
- Altitude profile simulation functionality (e.g. ‘Climb & Dive’) can be built in to the PC Touch Screen VCC upgrade option. Such functionality is valid only for altitudes of up to 100,000 ft / 19miles / 30km (pressures 10-4). See Altitude Test
- Systems for more details on ‘Climb & Dive’.
- Process Control Enclosure – Contains components necessary for controlling the system as well as logic and interfaces for the
- Vacuum Cycle Controller.
- Process Timer Control
- Status Indicators – Provide visual indication of system status.
- Vacuum Cycle Controller – Control ON/OFF buttons, main power switch.
- Control Valves are required with a VCC:
- Automatic Vent Valve – Automatic solenoid valve vents air or inert gas purge into chamber based on control input from Vacuum Cycle Controller.
- Proportional Valve – controls pumping to a certain rate for altitude profile simulation.
- Digital Pressure Gauge & Controller are required with a VCC
- Provides pressure display and set point valve control per integral Pressure Transducer data. Also provides pressure set-point relays that can be used for various system control functions.
- Mobile cart; or heavy duty in-built casters for the largest systems.
- Heating and/or cooling thermal plates/shelving and control:
for heating up to 150C, or 300C) (as illustrated in the Vacuum Oven System).
and/or for cooling to -150C. - Shelving (passive).
- Inert gas purge.
- Circulation fans.
- Mechanical feedthroughs such as shafts with or without rotation.
- Electrical feedthroughs for power and signals.
- Optical ports for optimal transmission of test equipment wavelengths
- Special coatings such as gold (e.g. for thermal shroud as in Fig. 2).
- Switchable, internal lighting
- Viewports / optical test ports (see Figs 2 & 3)
Abbess can help you. Successfully test your high-value inventory in our manual or automatic Space Simulation Systems.
To get an accurate quote for the system you need fill out our RFQ or call today!